Blog Posts
Corporate, Commercial / The Advantages of Utilizing Drilled Displacement Piles for Foundations at 101 Smith Place
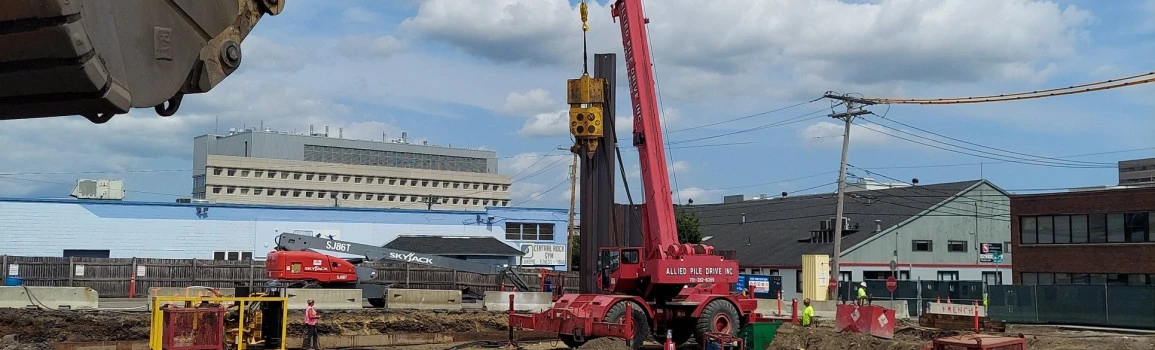
By Mike Lally, President, Sea & Shore Contracting, Inc. & Ben McConchie, Project Executive, Erland
During the preconstruction process, the Design Team issued documents for the 101 Smith Place project foundations that incorporated the use of regular concrete piles. Upon receiving these drawings, Erland Senior Estimator, Chris McHugh, engaged Sea & Shore Contracting, Inc. to determine a cost-effective alternative that would benefit the Owner’s budget and schedule. Based on the need for both significant compression and tension (uplift) loading, we evaluated value engineering options for deep foundations. Sea & Shore reviewed the geotechnical data provided by Haley & Aldrich, Inc., evaluated viable foundation options, performed an early pile load test program of the recommended option, and is now proceeding with full scale installation of foundation piles for the project.
We learned through this process that the soil profile across the site varies rather significantly with regard to the combined thickness of fill and organics, ranging from approximately 10ft at one end and nearly 45ft at the other. Below the fill and organics, deep deposits of medium dense marine sands and soft clay extend to depths beyond what were considered cost-effective for traditional driven piles to penetrate. We evaluated the potential for deep drilled displacement piles and concluded the soils were suitable for this technology. To demonstrate the load capacity and feasibility of this technique, Sea & Shore undertook an onsite test program including multiple static compression and uplift load tests which successfully demonstrated the capability of this foundation technique.
Drilled displacement piles are installed with tall, fixed leader rigs capable of delivering high-torque through the full depth of drilling. The pile is constructed by advancing a long (70ft, potentially longer) steel displacement mandrel using high rotary torque and a large hydraulic down force to push the mandrel into the ground. The combination of spinning and pushing leads to lateral displacement of the soils which densifies the soil mass and increases lateral and vertical load capacity. Once the drill mandrel reaches the required depth, a large diameter steel reinforcing bar is set within the hollow mandrel pipe and the mandrel pipe is fully filled with ready-mix concrete. The mandrel is then slowly retracted by pulling up with the drill rig and concrete flows from the bottom of the pipe to completely fill the borehole with pressurized concrete. Prior to starting each pile hole, an over-sized, sacrificial, cast-steel drill point is fit on the bottom of the mandrel to both keep soil from filling the hollow mandrel and to create a larger end-bearing surface at the bottom of the pile that increases vertical compression load capacity. Upon extracting the mandrel after the shaft is filled with concrete, the mandrel releases the tip that remains in place as a permanent element of the pile.
While the test borings describe a rather consistent layer of marine deposits below the fill and organics, we have encountered areas of the site where the soils appear to already be very dense. In areas where the high-torque and crowd-force of the rig have difficulty advancing the mandrel to required depth due to the very dense, granular soils, we have had to redesign piles (based on measured soil resistance) to keep project-pace and to prevent overstressing the rig. At times, we are shortening the embedded center-core bars based on measured soil resistance and installing two shorter length piles to provide sufficient pile capacity. The design team of McNamara Salvia Structural Engineers and Haley & Aldrich, Inc. have been great to work with and allow for these modifications as they’re needed.
From past experience with foundation drilling projects, Sea & Shore understands that productive foundation construction results from capable equipment operated by qualified personnel and prompt delivery and placement of concrete. A late concrete delivery can dramatically reduce efficiency and flow of the project. In order to ensure on-time concrete delivery, Sea & Shore and Erland teamed with inTerra Innovation. inTerra is a specialty construction materials company focused on providing innovative solutions for the design, manufacture, delivery and installation of products for the construction industry. They have developed a system that allows them to produce high volumes of diverse cementitious products on a jobsite with mobile mixers. This high-quality concrete product eliminates concerns for late deliveries that may compromise the fluidity or caliber of the concrete as well as impact daily production quantities. inTerra has been a great partner and consistently provided extremely dependable onsite service throughout this process.
Utilizing this approach offers a handful of advantages. Drilling the displacement piles provides a significant savings to the project of both time and construction cost. We attribute the cost effectiveness to the use of cast concrete piles. This type of pile provides the support that the foundation needs to resist both the uplift and the compression loads. Displacement drilling also avoids the need to manage drill soil cuttings and potential high costs associated with offsite disposal of potential contaminated soils since no soils are generated during drilling. Instead, the specialty drill mandrel promotes lateral displacement/compaction of soil around the drill holes. Additionally, this technique causes minimal disturbance to the surrounding abutters. By involving inTerra into our daily activities, the project has significantly reduced typical construction traffic in the project area which is also a plus. Weekly deliveries to the site are reduced to 3 to 4 loads of sand/stone aggregate, 2-3 bulk tanker loads of cement, and one flatbed trailer delivering pile reinforcing steel to the job. There are days that no deliveries are made to the site, which is uncommon for full scale deep foundation construction.
A total of 500 drilled displacement piles will be installed. Erland and Sea & Shore look forward to completing this process by the end of the year.
For any questions regarding this topic, please contact Ben McConchie at bmcconchie@erland.com.