Blog Posts
AT/LS / Lab & Cleanroom Construction: What You Need to Know
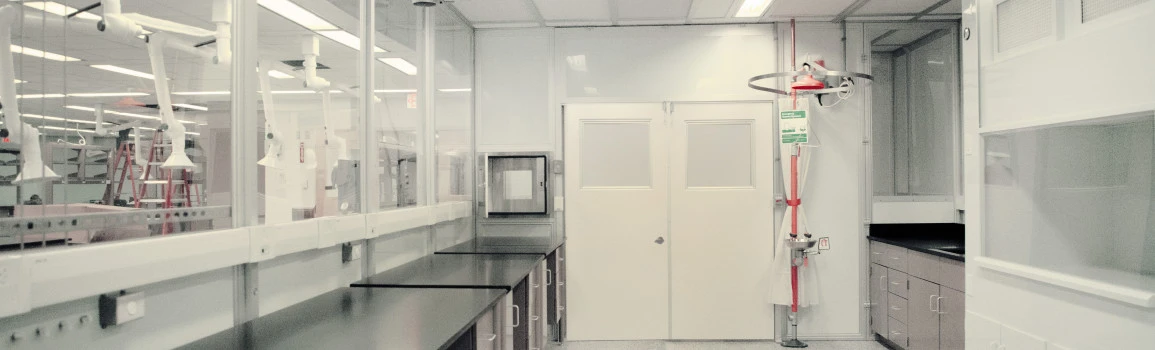
Authored by Gregg Conboy, Senior Project Manager
Understanding the goals of our clients is the key to a successful project. When it comes to lab and cleanroom construction, this is even more critical. We come in early and ask the questions that will allow us to meet your current and future needs. This process is known as program development.
During the program development phase, we meet with the client, facility management team, and end-users to gather input, set expectations, and formalize the decision-making process. In some cases, a Steering Committee will be established or a sole decisionmaker will be for the final approval. Doing this ensures the project’s schedule, quality, budget, and requirements are successfully met.
One major component of program development is establishing the equipment and utilities needed to accurately build your lab or cleanroom environment in accordance with your budget and schedule. Here’s what you need to know about Erland’s role in this process.
Research labs, and at times cleanrooms, are often very densely populated with equipment. To ensure the space is laid out properly, things like process exhaust drops and utility requirements need to be captured during the programming phase. We utilize an equipment matrix to do this. An equipment matrix is a document and one of the most important steps in developing the basis of design for a project. It helps identify the equipment, utilities, and infrastructure required for proper utilization and operation. The equipment matrix is ultimately used to ensure the design team, construction manager, and end-user are collaborating and meeting all the project’s requirements. This tool also helps determine connection sizes and if there is point-of-use isolations, regulation, or filtering requirements for the various process utilities.
When reviewing equipment, electrical requirements need to be considered as well. It is important to understand what, if anything, needs to be on UPS power, life safety power, optional stand-by power, or legally required generator power. Additionally, a chemical list needs to be provided by the client during programming to ensure components used in the fit-out, such as flooring, are compatible or have resistance to the chemicals being used. Reviewing product compatibility with the chemicals used in a lab or cleanroom environment also helps the design team to determine if there are any special code requirements that need to be incorporated into the design.
In most lab and cleanroom environments, several process utilities may come out of the ceiling to service equipment. It is critical that the placement of the utilities be coordinated with the equipment for access and serviceability. We produce extensive coordination drawings and utilize a BIM model to carefully lay out all the necessary piping in precise detail, co-locate the MEPs with each designated tradesperson, and create a model so accurate, our subcontractors can prefabricate much of the work in advance. This not only ensures everything fits but also allows enough space for equipment to be serviced, replaced, or expanded.
For any questions regarding this topic, please contact Gregg Conboy at gconboy@erland.com.