Blog Posts
Erland / Proactive Planning to Ensure Quality
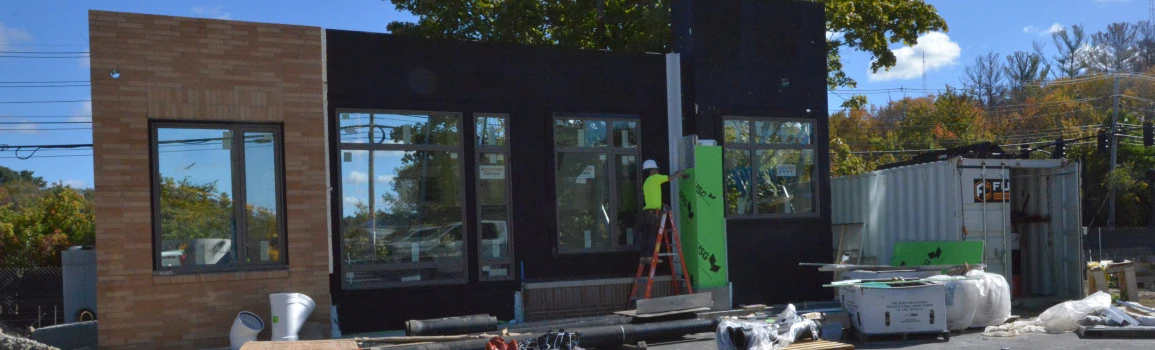
By Matt Combs, Project Executive, Quality Committee Chair
In construction, clients expect the highest level of quality in the product and workmanship of their new building or renovation. As construction manager, it is Erland’s job to ensure a project is delivered to these standards. Since our inception in 1977, we’ve worked on improving our processes and creating best practices that allow us to build to that high level of quality.
In the late 90s, with the company growing geographically, executives established a task force to develop a comprehensive Quality Control Program to ensure each team's project approach was consistent with the "Erland Way”. Since then, an internal committee has been created to refine the program, develop a written quality manual, and perform site reviews throughout the project's lifetime to confirm that all processes are being followed to the standards we set.
Planning starts early on by setting expectations and assessing the risks with the client, architect, engineer, and quality committee. During our premobilization meeting for each project, Erland team members take a proactive approach to quality by filling out and reviewing a risk assessment matrix. The teams work to identify obstacles that, if left unattended, have the potential to cause the project significant issues. These issues may then cause damage in the form of impacts to cost, schedule, safety, relationships, reputation, or a combination thereof. The team assigns values for the likelihood and impact of each identified item and then comes up with proposed measures that can be taken to manage those perceived risks proactively. The overall goal is that this approach helps the team mitigate or minimize potential threats to the project’s budget and schedule upfront.
Peer reviews are also an integral part of our quality program. Outside agencies are consulted to perform an envelope review and a mechanical peer review. This is because we have found that two of the most significant potential warranty callback risks concern those areas. Utilizing experts in the field to perform analysis of the documents can often uncover items that may have either not been detailed or considered. Whether something is covered by warranty or not, issues after turnover present headaches for all stakeholders. It’s great to have a warranty, but even better not to need to use it! This process aims for the latter to achieve a better result for the owner.
Another major step in ensuring quality is mock-ups. Every new building we construct gets a small-scale configuration of exterior materials. Starting this procedure early in the project not only helps drive the owner and architect to make decisions during an era of long lead times but gives you ample opportunity to test the quality of the product, work through constructability issues, and have time to react to unforeseen problems. Mock-ups of other key project elements may also be performed if the team perceives a potential risk (think specialty flooring, ceilings, etc.) The goal of any mock-up is to set expectations with all project stakeholders and prevent possible schedule delays later on.
At project completion, the team will schedule a debrief to share lessons learned and provide subcontractor evaluations. Determining what works and what doesn't goes a long way toward the success of the next partnership. Our quality goal is to ensure we continuously improve on what we do to deliver the best end product possible for our clients.
For any questions regarding this topic, please contact Matt Combs at mcombs@erland.com.