Blog Posts
ATLS / Recharging the Future: Transforming cGMP Facilities into Battery Manufacturing Spaces
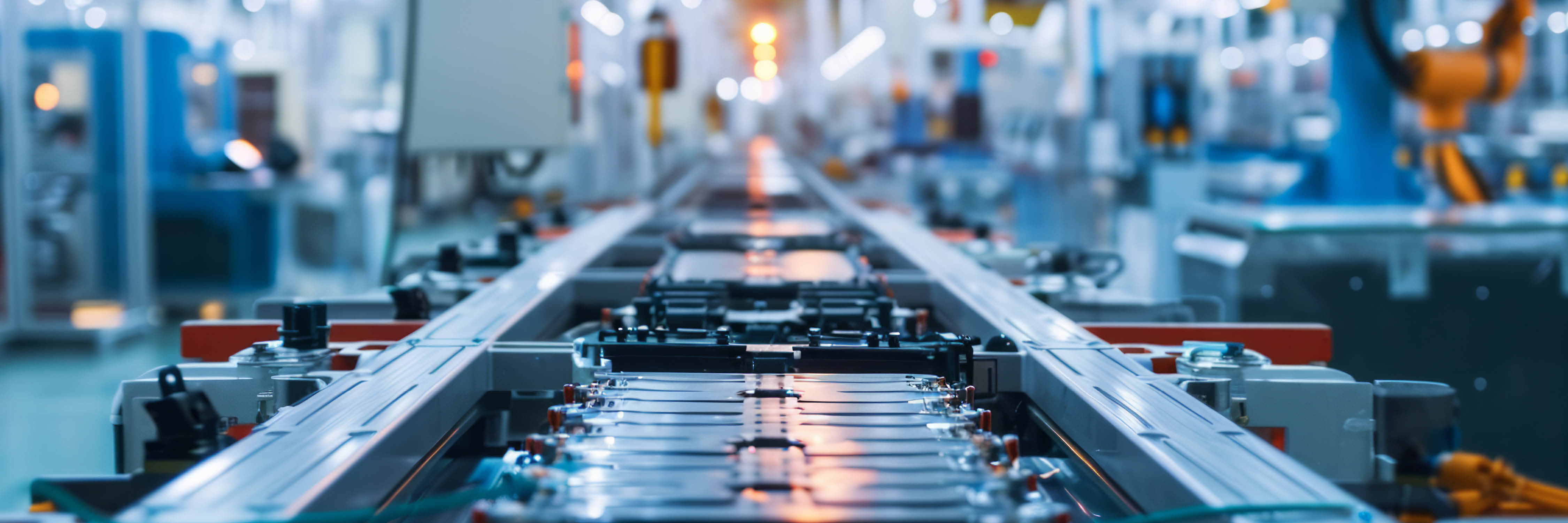
By Kyle Dupell, AT/LS Group Project Executive
As demand for clean energy solutions surges, battery manufacturing has emerged as a cornerstone of innovation. The CHIPS Act has accelerated this movement, creating significant opportunities for facilities to pivot toward battery production. At Erland Construction, we’ve spent 48 years helping clients adapt and thrive in evolving industries. Our team understands the challenges of converting existing cGMP (current Good Manufacturing Practice) facilities into advanced battery manufacturing spaces—and we’re here to help you meet them head-on.
Converting a cGMP facility into a battery manufacturing space requires a deep understanding of both existing infrastructure and the unique needs of battery production. At Erland, we have decades of experience working in advanced technology environments, including cleanrooms and highly specialized manufacturing facilities. We assess your facility to ensure that production workflows are efficient and meet the demands of battery manufacturing. Battery production places significant demands on power, ventilation, and cooling systems. We’ll enhance your facility’s utilities to meet these needs while minimizing disruption.
Battery manufacturing comes with specific safety challenges, from handling hazardous materials to maintaining strict environmental controls. Erland has the expertise to navigate these complexities:
- Regulatory Compliance: We integrate fire suppression systems, explosion-proof fixtures, and containment solutions that meet NFPA and OSHA standards.
- Enhanced Cleanrooms: For facilities requiring cleanroom environments, we align with ISO standards to ensure contamination control critical to battery production.
We know that in today’s fast-paced market, time is everything. With Erland’s collaborative delivery methods, including our COLAB Solutions model, we fast-track project schedules without compromising quality. By partnering with you early, we streamline decision-making and ensure that your facility is up and running quickly to meet the demands of this rapidly growing market.
Sustainability is a priority for us—and likely for your organization too. When converting cGMP facilities, we look for ways to:
- Integrate energy-efficient systems and renewable energy sources, such as solar panels.
- Reuse materials and systems wherever possible to reduce waste and costs.
Our team builds for the long term. By recommending modular design and advanced digital facility management tools and equipment, we ensure your manufacturing space remains flexible and ready to adapt to future advancements in battery technology or other market needs.
Navigating incentives tied to the CHIPS Act and regional programs can be complex, but they are key to maximizing your investment. Erland will collaborate with your regulatory experts to align your project with these opportunities while assisting with ensuring compliance.
Whether you’re preparing to pivot your facility to battery production or exploring how to leverage the CHIPS Act, we’re ready to bring nearly five decades of experience to your project. Let’s recharge the future together. Contact us today to learn how we can help you convert your cGMP facility into a cutting-edge battery manufacturing space.
For any questions regarding this topic, please contact Kyle Dupell at kdupell@erland.com.