Blog Posts
ATLS / Navigating the Intricacies of Constructing cGMP-compliant Facilities: The Crucial Role of a Program Development Manager
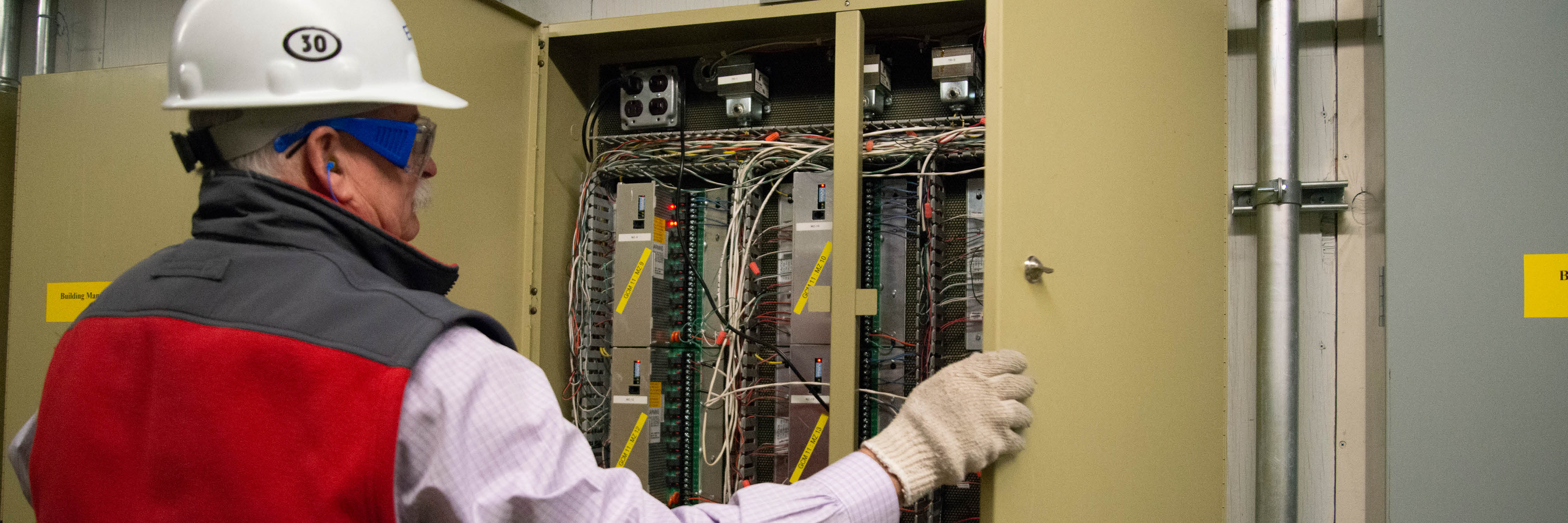
By Gregg Conboy, Program Development Manager
Constructing a Current Good Manufacturing Practice (cGMP) facility is a highly specialized process that requires a detailed and methodical approach to meet stringent regulatory standards. As a Program Development Manager at Erland, my role is pivotal in ensuring that every stage, from concept to commissioning, is executed flawlessly. Here’s a closer look at how we navigate the complexities of constructing a cGMP facility and the critical tasks I undertake in Commissioning, Qualification, and Validation (CQV) management.
Analyzing the Spatial Layout
One of my initial functions for a cGMP renovation project is to analyze the spatial layout of the proposed facility or space meticulously. This involves:
- Identifying Available Resources: Assessing the existing infrastructure is crucial. This involves a thorough investigation of the building’s mechanical, electrical, plumbing, and fire protection systems and comparing them to the requirements of the desired new program.
- Supplementary Additions: I evaluate what additional elements can be incorporated to enhance service and function. This may involve integrating new systems or upgrading existing ones to meet cGMP standards.
Collecting & Analyzing End-User Data
Collaboration with end-users is key to understanding their specific needs and ensuring the facility’s program is both functional and efficient. This involves:
- Establishing Standards: Working with end-users and EH&S to establish laboratory, manufacturing, and support space construction and operations standards.
- Performance Criteria: Identifying the building system performance criteria to ensure the facility operates within the required parameters.
- Due Diligence Studies: Conducting thorough due diligence studies to identify any potential issues that could impact the project.
- Program Strategy Validation: Validating existing program strategies to ensure alignment with project goals and regulatory requirements.
Establishing the Basis of Design, Budget, & Schedule
Early discussions about design, budget, and schedule are crucial. By engaging in these conversations at the outset, we can define the overall program effectively, ensuring that we meet your unique needs and adhere to cGMP standards. This proactive approach allows us to align our plans with your vision and regulatory requirements from the very beginning.
- Basis of Design: Establishing detailed specifications that guide the construction process. This involves considering several key elements to ensure the facility meets all operational requirements:
- Flexibility: The facility must be adaptable enough to accommodate increased water, gas, specialized (or processed) utilities, and sanitary services, as well as additional equipment and manufacturing components.
- Room Size: Rooms should be large enough to allow for safe and ergonomic operation but small enough to keep air treatment costs down. It’s important to note that HVAC systems can account for 70–80% of a pharmaceutical manufacturing facility's electricity consumption.
- Waste Removal: Effective waste management is essential. Waste must be removed from the facility and kept separate from raw materials and finished products.
- Technical and Functional Specifications: Defining these specifications ensures that every aspect of the facility meets the required standards.
- Process & Instrumentation Lists: Developing these lists helps in maintaining accuracy and consistency in processes.
- Routing Facilities with Dimensions: Proper routing ensures optimal flow and efficiency.
- Isometrics of Critical Facilities/Process Suites: Creating isometric drawings of critical facilities/process suites provides a clear and detailed view of the layout.
- Budget Management: Developing a comprehensive budget that efficiently allocates financial resources, avoiding cost overruns.
- Scheduling: Coordinating with all stakeholders to develop a realistic timeline with key milestones and deadlines.
Tool Matrix Development
Developing a tool matrix involves identifying all the production equipment needed for your project. This comprehensive planning ensures that necessary resources are available when needed, minimizing delays and disruptions.
In addition to the Tool Matrix, I use Piping & Instrumentation Diagrams (P&ID) and Process Flow Diagrams to aid in the planning and coordination of your facility’s process systems program.
Piping & Instrumentation Diagram (P&ID)
The Piping & Instrumentation Diagram (P&ID) is a crucial document in the construction of a cGMP facility. It provides a detailed graphical representation of the piping systems and instrumentation in the facility. This includes:
- Piping Layouts: Showing the arrangement of pipes, including the dimensions, materials, and flow direction.
- Instrumentation Details: Identifying all instruments used to measure and control the process parameters.
- Interconnection Diagrams: Illustrating the connections between different pieces of equipment and systems.
Process Flow Diagram (PFD)
The Process Flow Diagram (PFD) outlines the flow of materials and processes within the facility. It includes:
- Process Steps: A step-by-step depiction of the manufacturing process.
- Flow Rates: Indicating the flow rates of materials at different stages.
- Equipment List: Listing all equipment involved in the process.
- Control Systems: Showing the control systems used to monitor and regulate the process.
Long-Lead Identification & Early Procurement
Identifying long-lead items early in the planning process is crucial for maintaining the project schedule. By securing these items in advance, we avoid potential delays and keep the project on track.
Ensuring Compliance & Quality
My role in compliance and quality management extends beyond planning and coordination. Ensuring construction is performed in accordance with regulatory standards is an ongoing process that requires vigilance and attention to detail. This includes:
- Quality Control/Quality Assurance Program: Establishing a robust QC/QA program to monitor all phases of construction and ensure compliance with cGMP standards, including high-purity process piping and weld logs.
- Commissioning: Verifying that all systems and components are designed, installed, tested, and operated according to operational requirements.
- Qualification: Documenting that equipment, systems, and processes meet specified requirements.
- Validation: Working with a third-party consultant to ensure that the facility produces products that consistently meet predetermined quality criteria.
At Erland, we pride ourselves on our ability to deliver high-quality pharmaceutical environments that meet and exceed industry standards. As a Program Development Manager, my expertise and dedication ensure that every cGMP facility we construct is safe, compliant, and efficient and enhances your operations.
For any questions regarding this topic, please contact Gregg Conboy at gconboy@erland.com.